
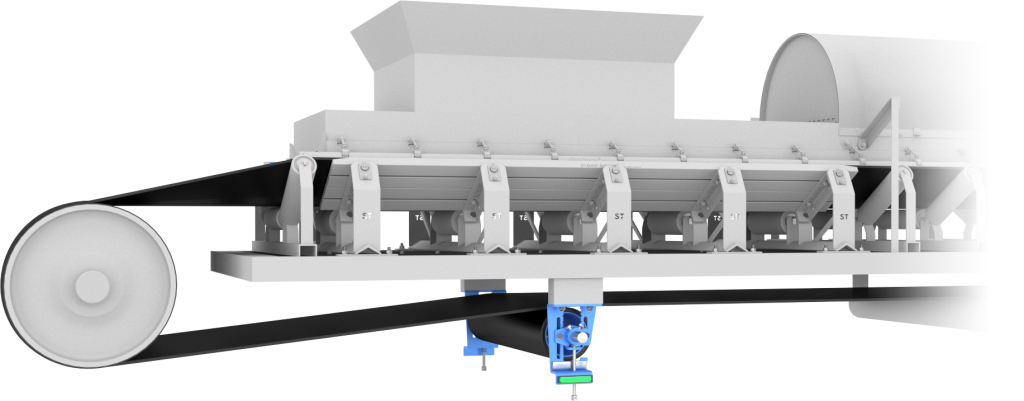
The E-PrimeTracker answers this question simply and comprehensively. Equipped with additional sensors, it works remotely and sends its data on the belt running status to monitoring systems.

Is everything okay with the conveyor belt?
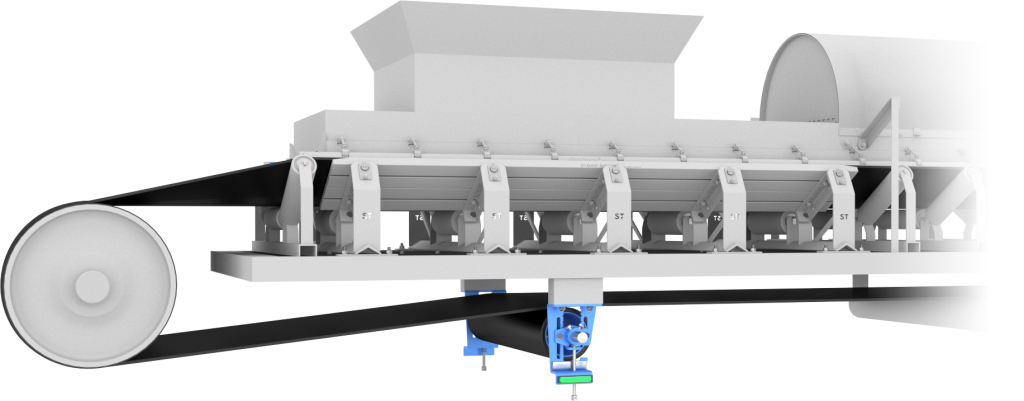
The E-PrimeTracker answers this question simply and comprehensively. Equipped with additional sensors, it works remotely and sends its data on the belt running status to monitoring systems.
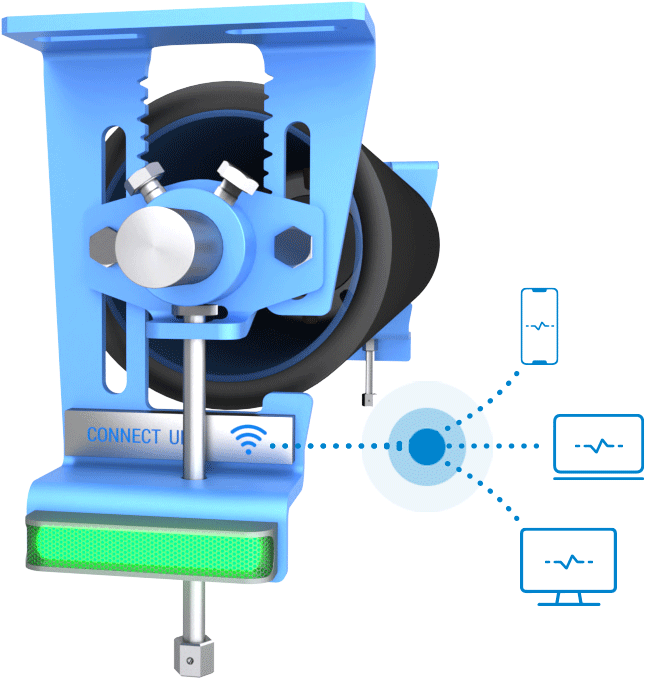
Local evaluation,
data transmission via radio
Robust sensors are installed in the tracker. In addition to monitoring for misalignment, they can also capture other key and meaningful metrics, such as belt position, belt speed, and the condition of the belt splicing. The processed sensor data can also be easily integrated into standard preventative maintenance systems, and accessed through the E-PrimeTracker mobile app. Based on the transmitted data, the user can identify service needs, as the sensors can reliably detect changes and issue a warning message early, before major damage or unscheduled belt downtime occurs.
In addition, the E-Prime Tracker collects the recorded data and documents it. Based on this data, the user can, for example, optimize the operation of the belt and thus extend its lifespan.
.
Tracking activity history
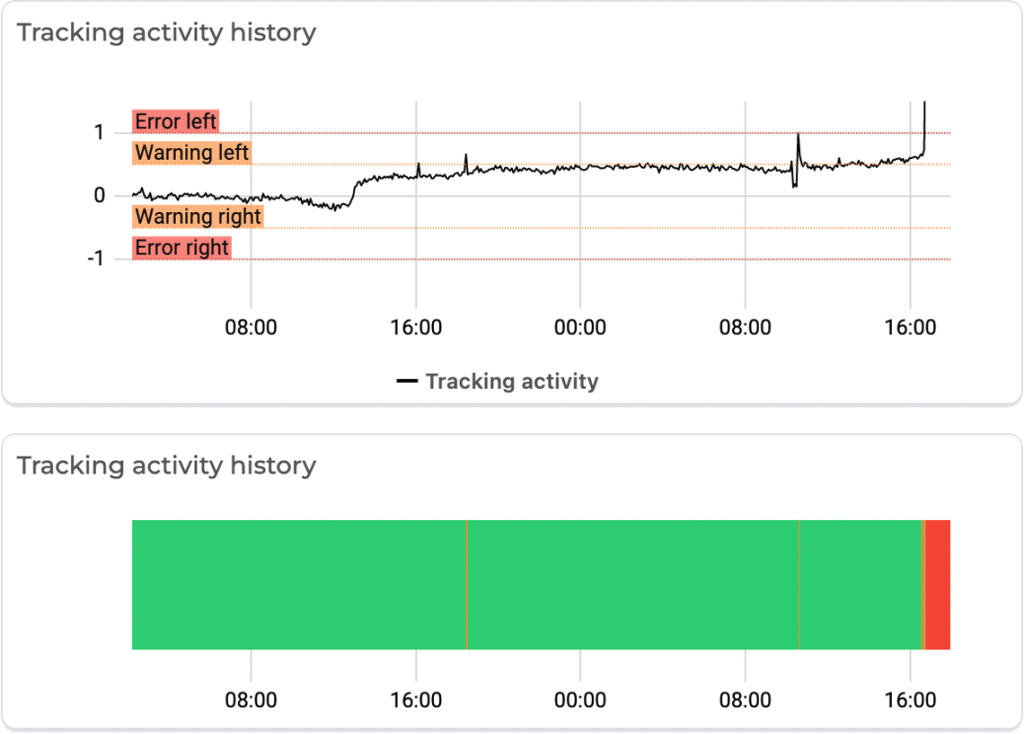
Sound pressure level
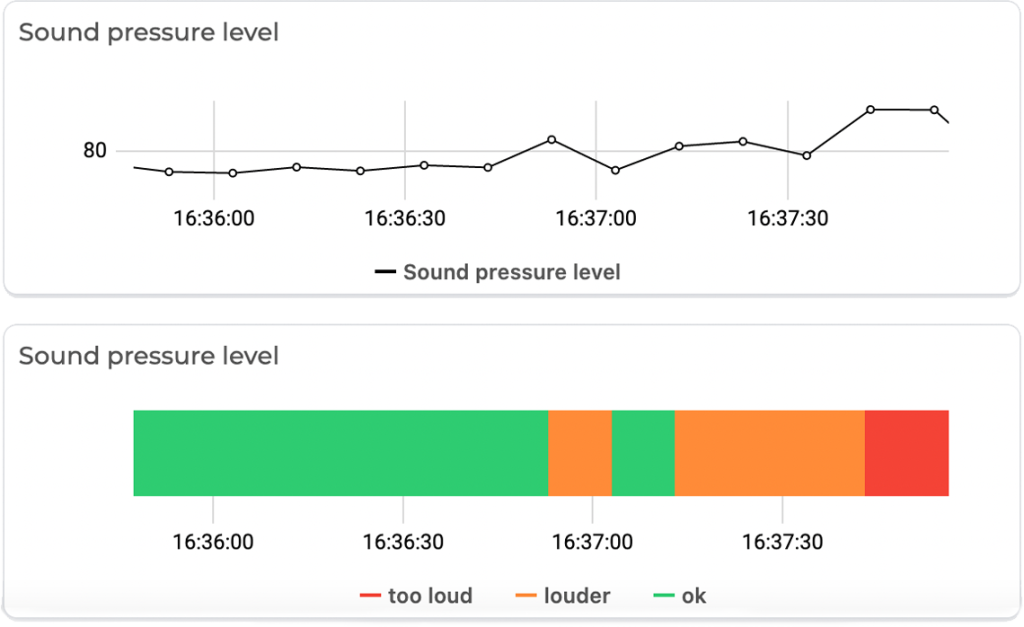
Local evaluation,
data transmission via radio
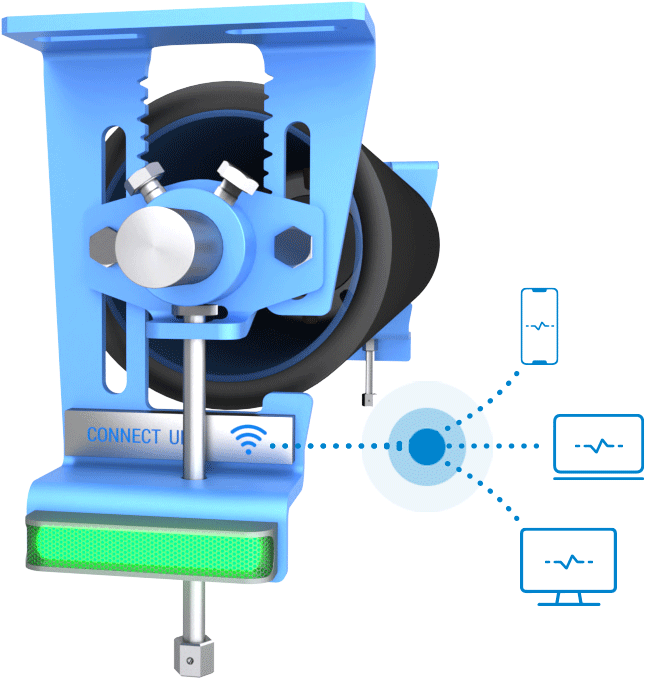
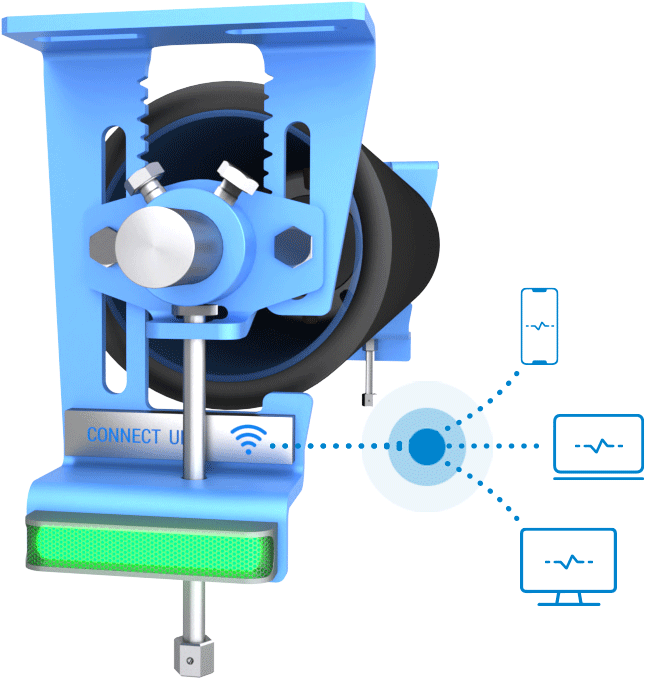
Robust sensors are installed in the tracker. In addition to monitoring for misalignment, they can also capture other key and meaningful metrics, such as belt position, belt speed, and the condition of the belt splicing. The processed sensor data can also be easily integrated into standard preventative maintenance systems, and accessed through the E-PrimeTracker mobile app. Based on the transmitted data, the user can identify service needs, as the sensors can reliably detect changes and issue a warning message early, before major damage or unscheduled belt downtime occurs.
In addition, the E-Prime Tracker collects the recorded data and documents it. Based on this data, the user can, for example, optimize the operation of the belt and thus extend its lifespan.
Tracking activity history
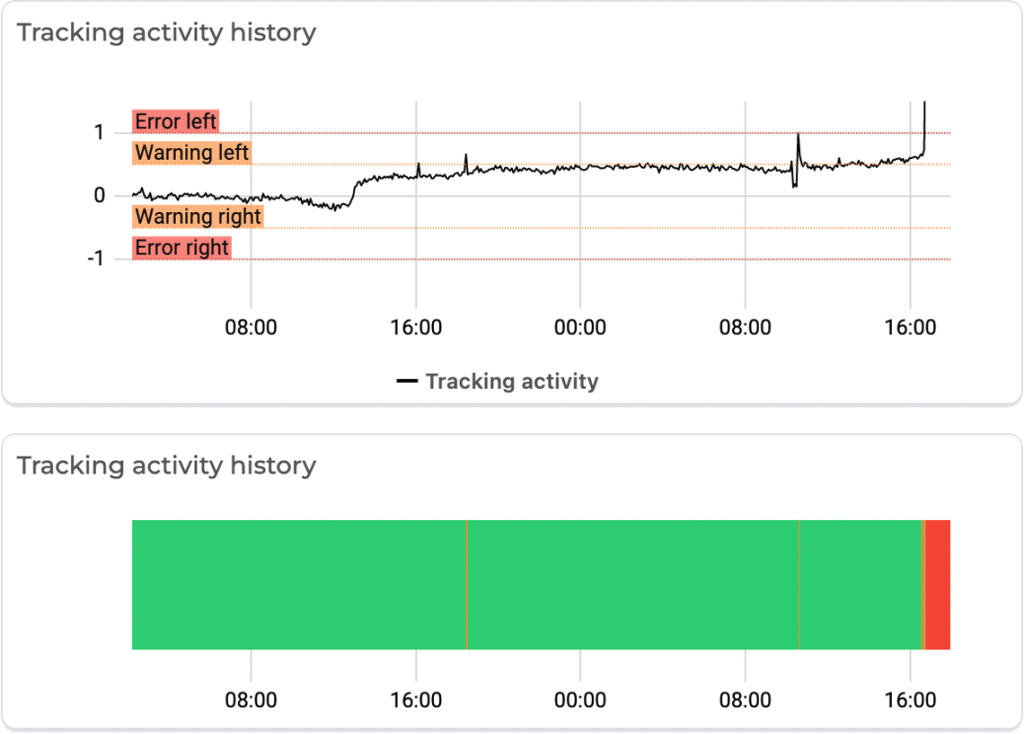
Sound pressure level
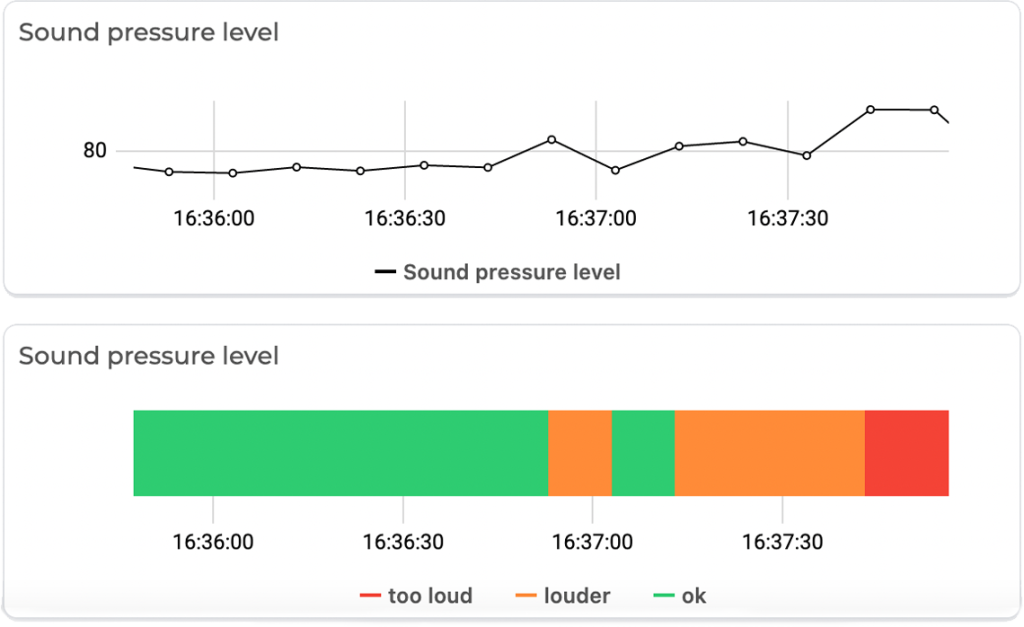
Optical condition control
Sensors integrated into the E-PrimeTracker detect the position of the tracker and therefore the status of the belt operation. The detected state is displayed directly on the device through a light signal. Based on the displayed colors of green, yellow, and red, employees can recognize the condition of the belt operation and respond to any fluctuations in alignement (yellow). The red warning signal indicates that immediate inspection is necessary to avoid any belt damage or downtime.
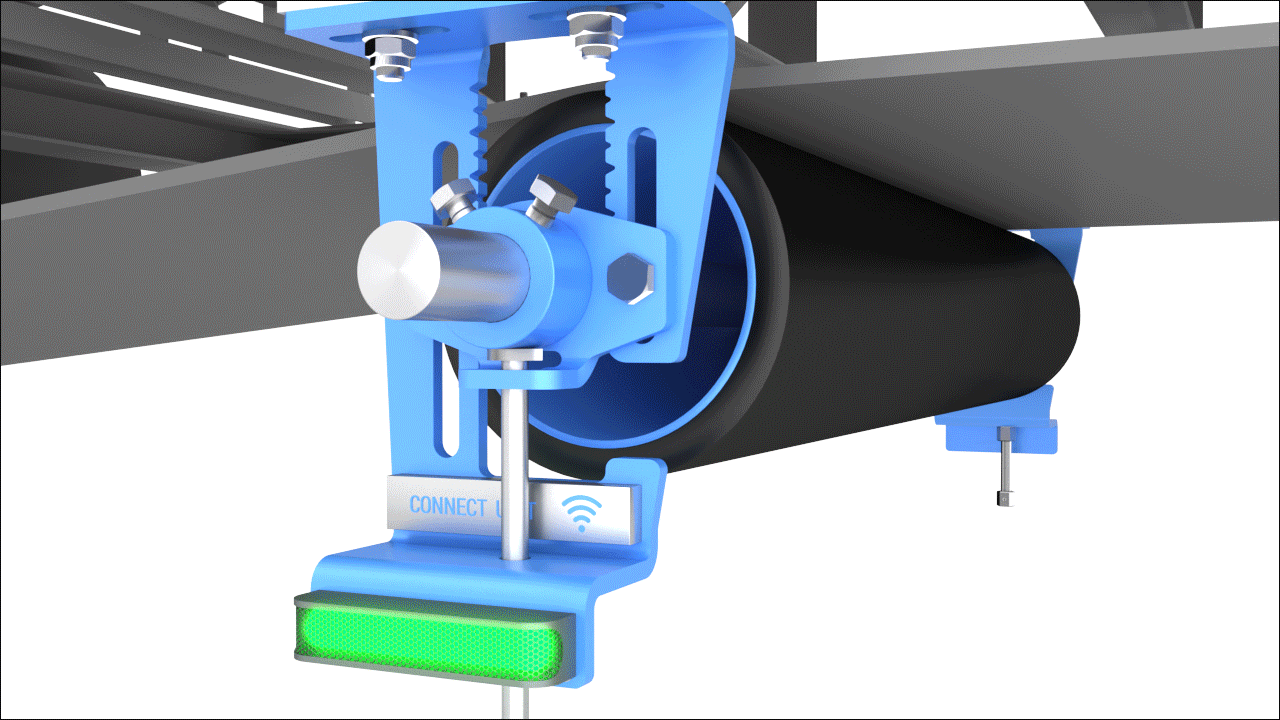
Optical condition control
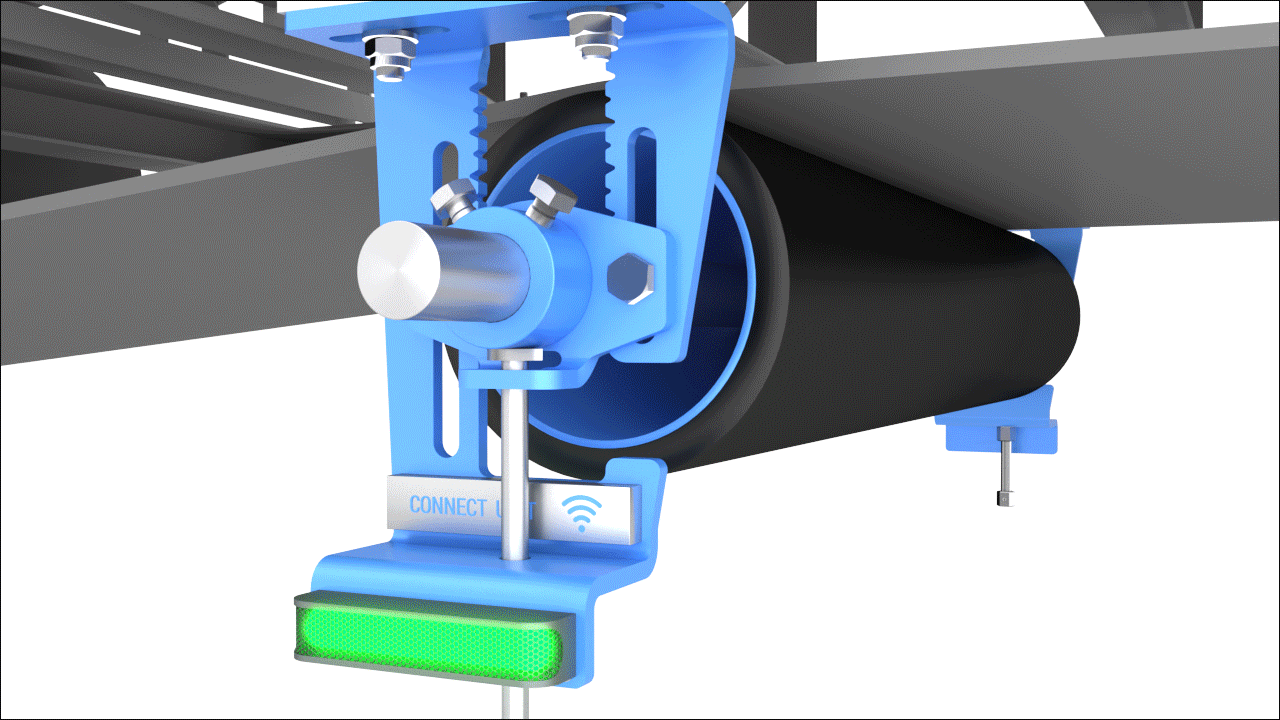
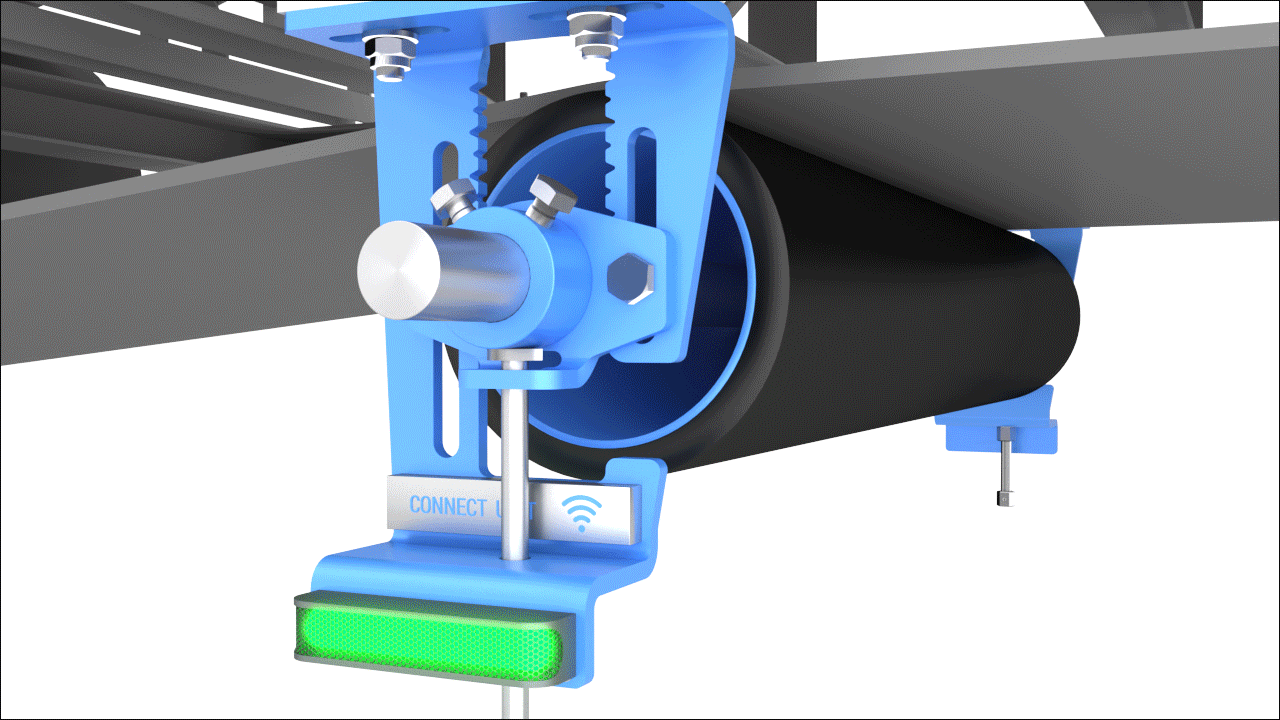
Sensors integrated into the E-PrimeTracker detect the position of the tracker and therefore the status of the belt operation. The detected state is displayed directly on the device through a light signal. Based on the displayed colors of green, yellow, and red, employees can recognize the condition of the belt operation and respond to any fluctuations in alignement (yellow). The red warning signal indicates that immediate inspection is necessary to avoid any belt damage or downtime.
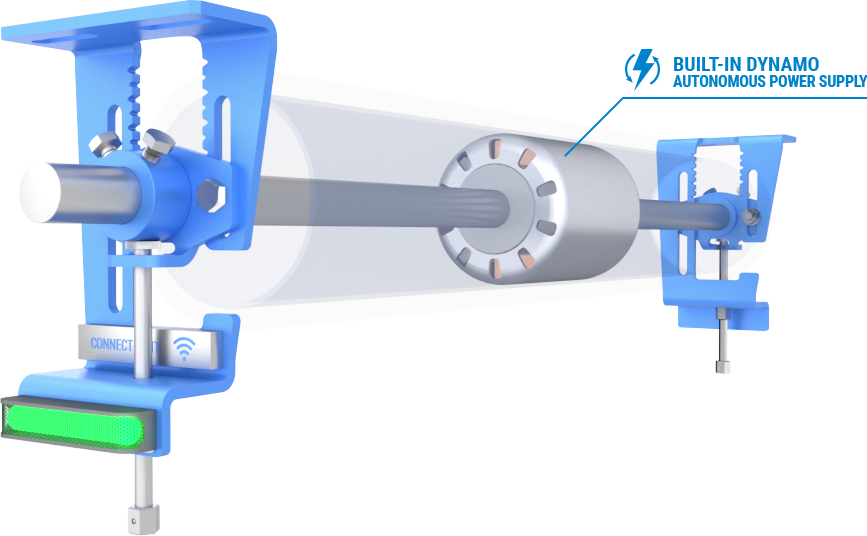
Autonomous power supply
The E-PrimeTracker contains an integrated generator that produces the energy required for operation. This means that the system operates completely autonomously.
Autonomous power supply
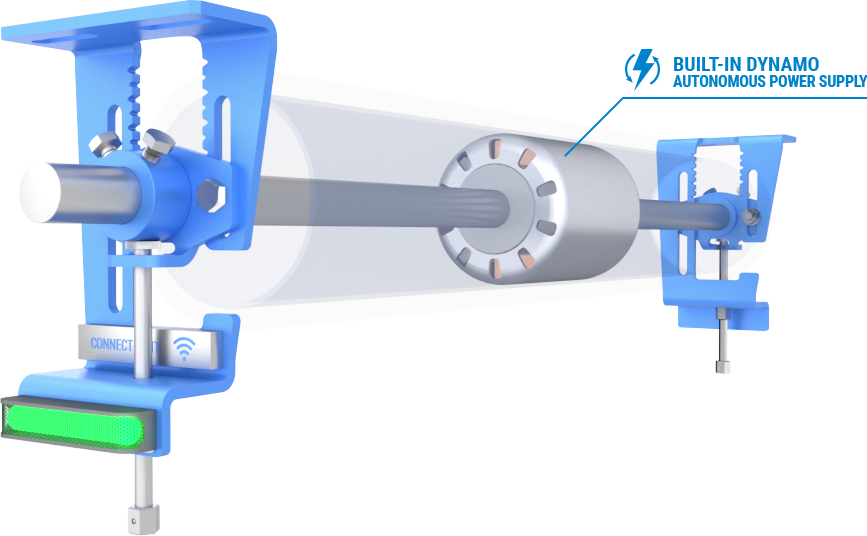
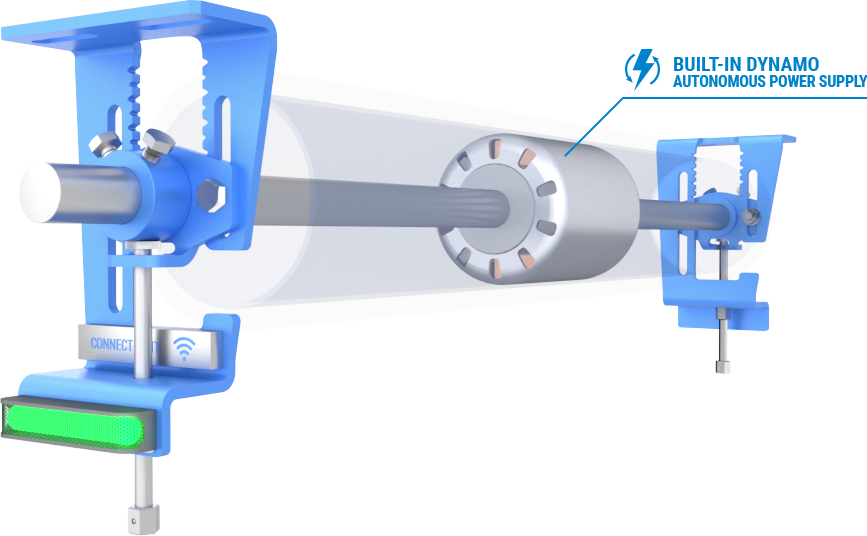
The E-PrimeTracker contains an integrated generator that produces the energy required for operation. This means that the system operates completely autonomously.
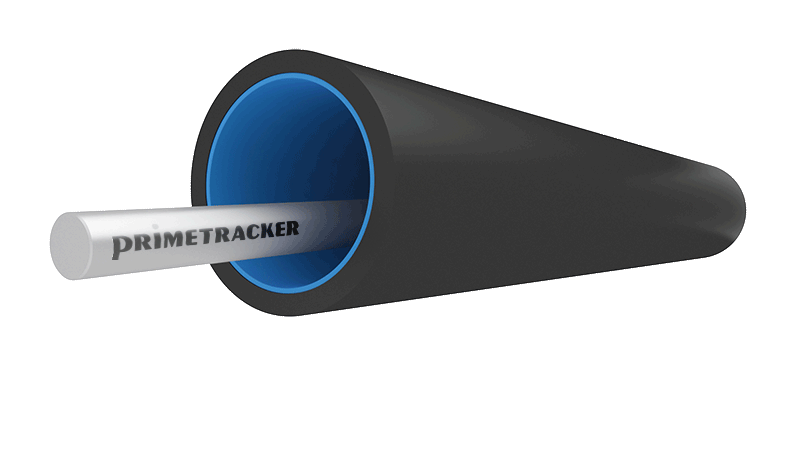
Cylindrical tracker with misalignment correction
Unlike similar systems, the E-Prime Tracker is not conical, but cylindrical in shape. The tracker is centrally mounted on an axis and can therefore swing freely in any direction within a 360° radius during operation to respond sensitively and directly to the slightest misalignment and correct it to ensure optimal belt operation.
Balanced
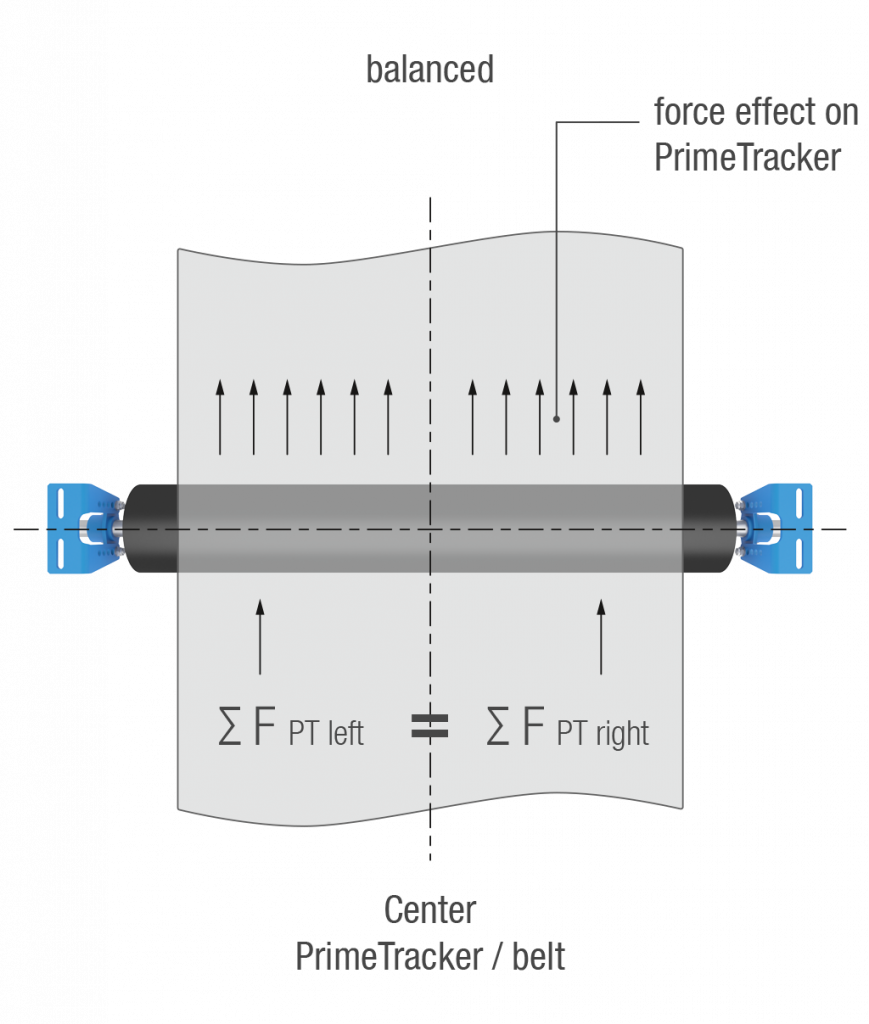
In case of slight misalignment
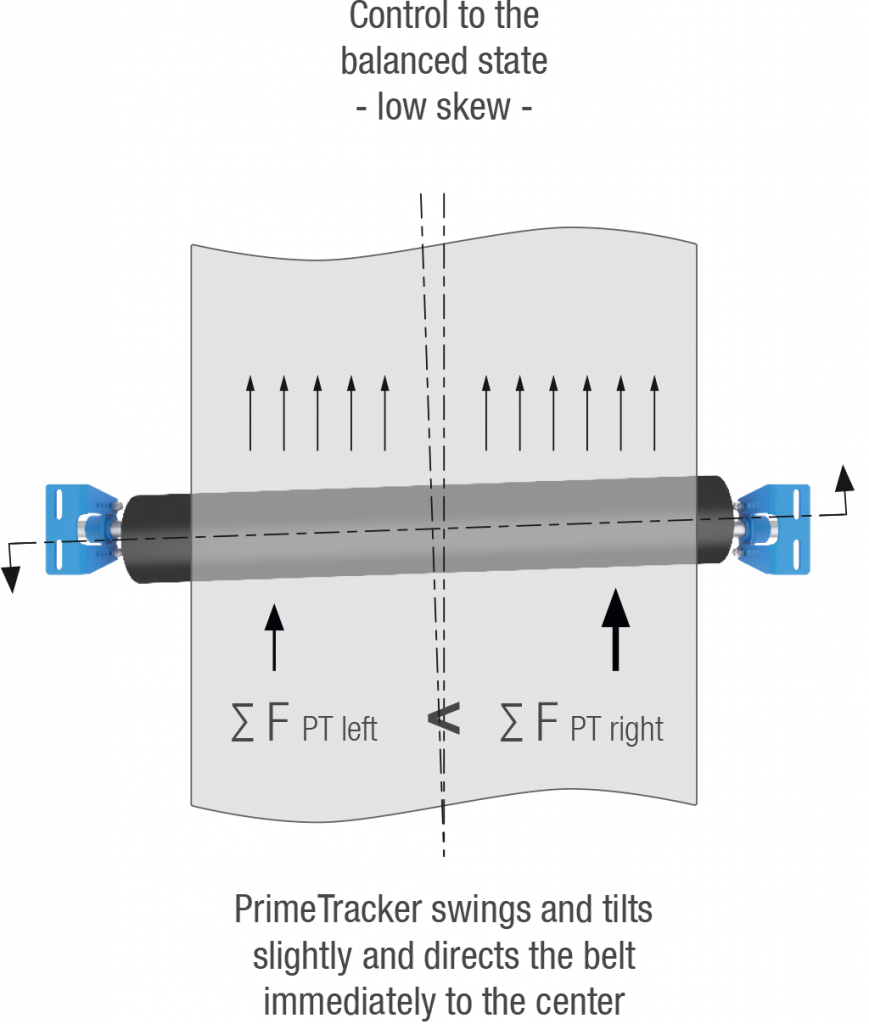
In case of strong misalignment
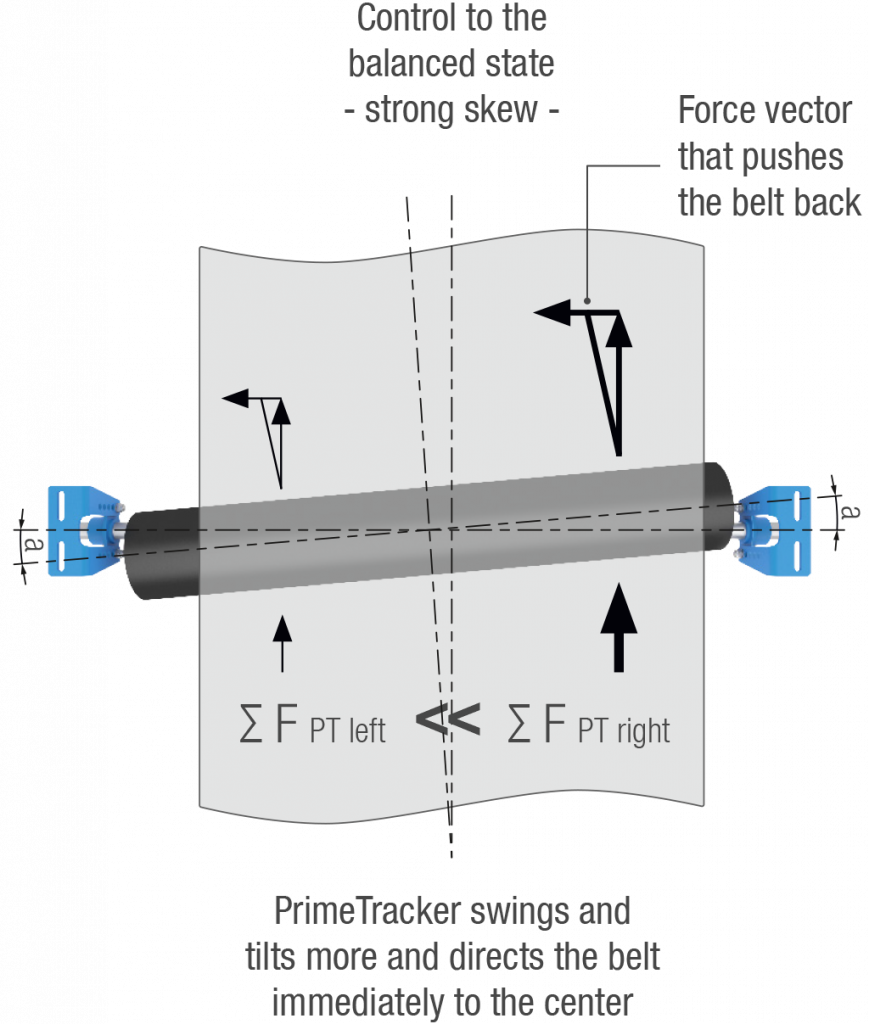
Balanced
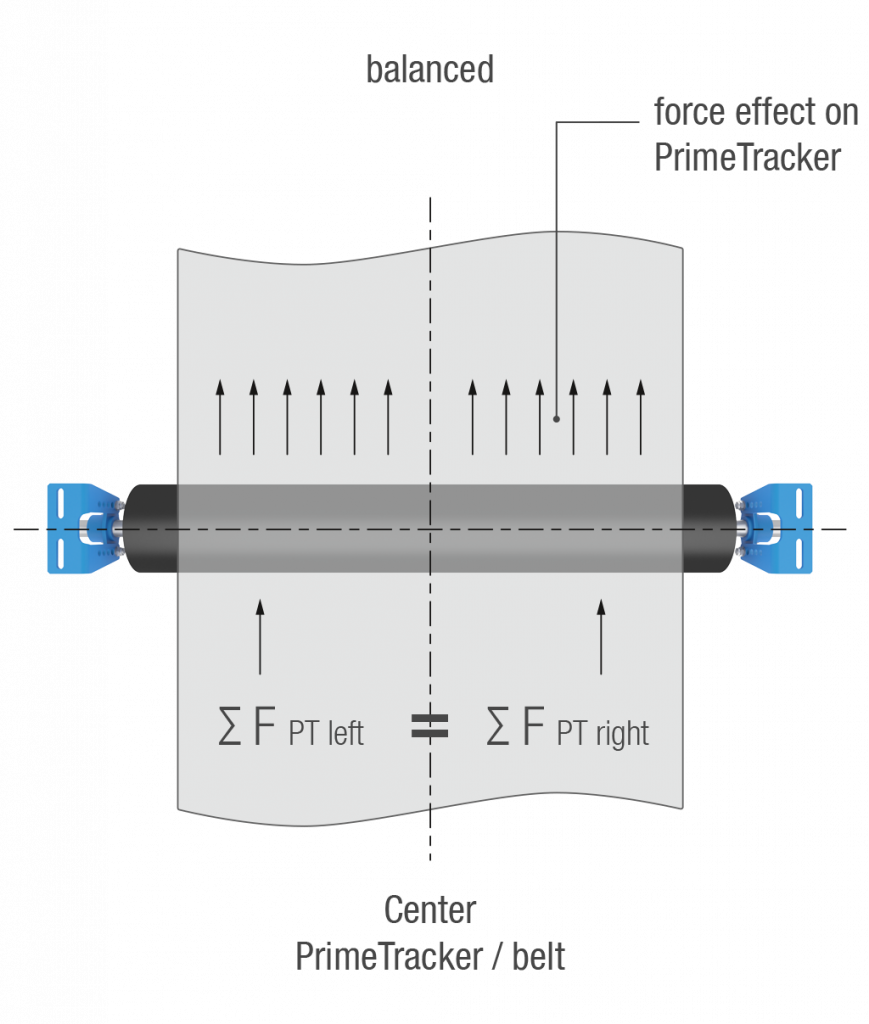
Cylindrical tracker with misalignment correction
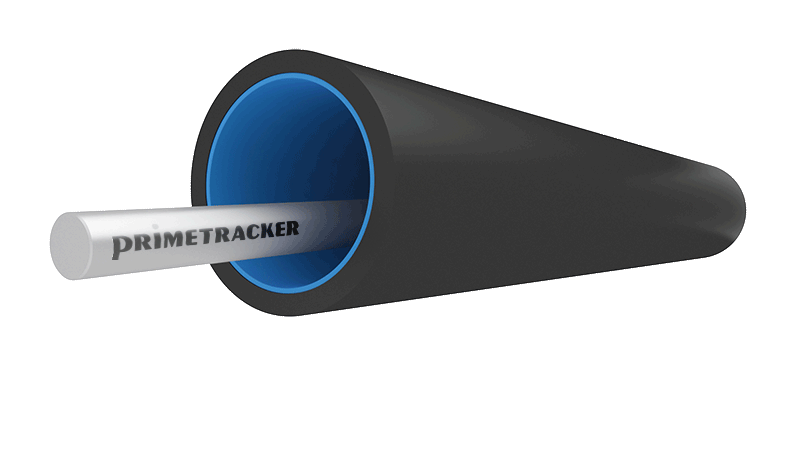
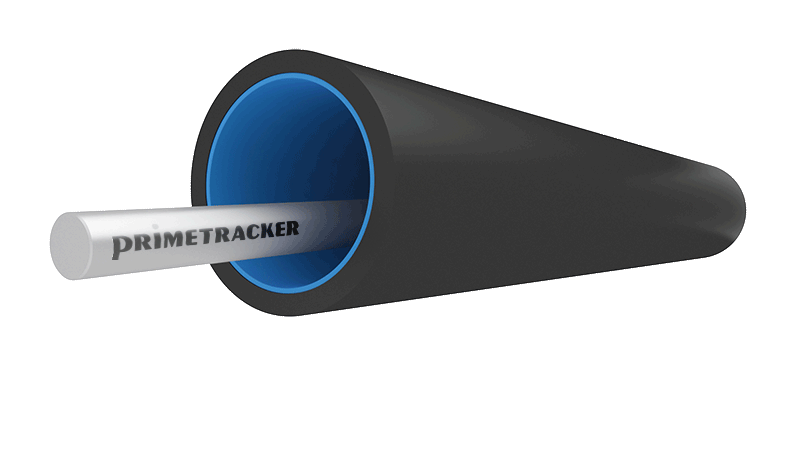
Unlike similar systems, the E-Prime Tracker is not conical, but cylindrical in shape. The tracker is centrally mounted on an axis and can therefore swing freely in any direction within a 360° radius during operation to respond sensitively and directly to the slightest misalignment and correct it to ensure optimal belt operation.
Balanced
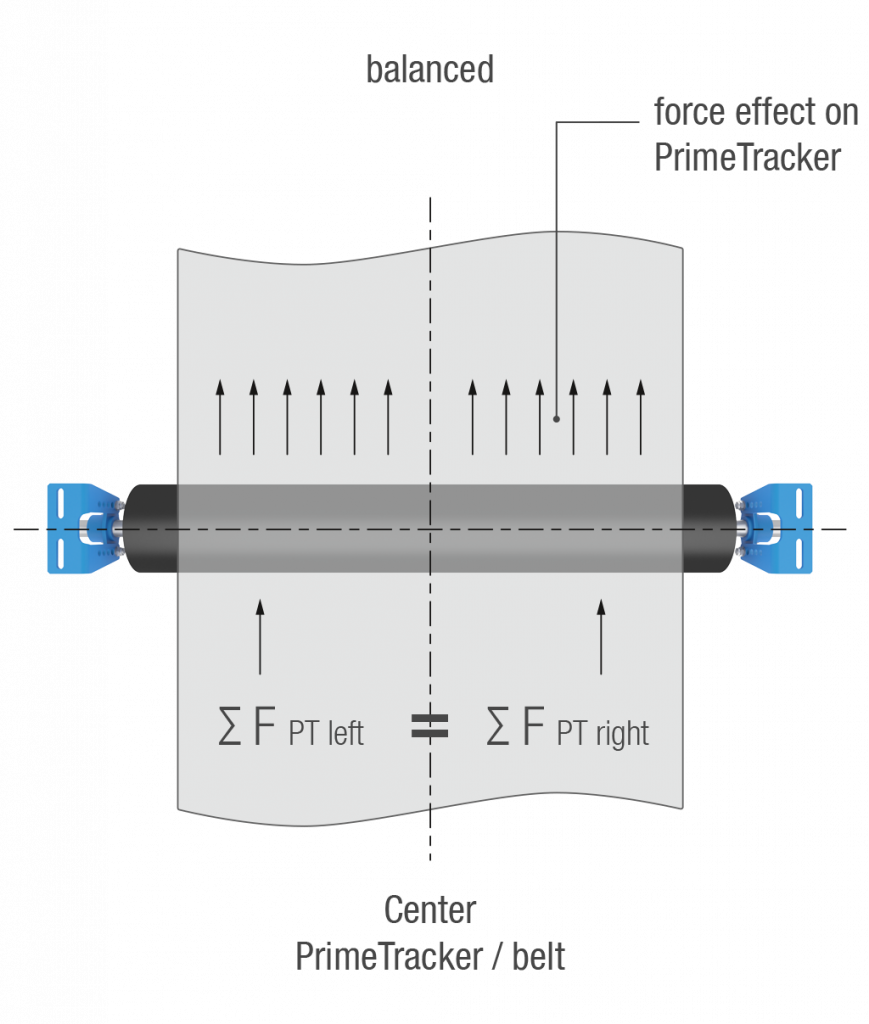
In case of slight misalignment
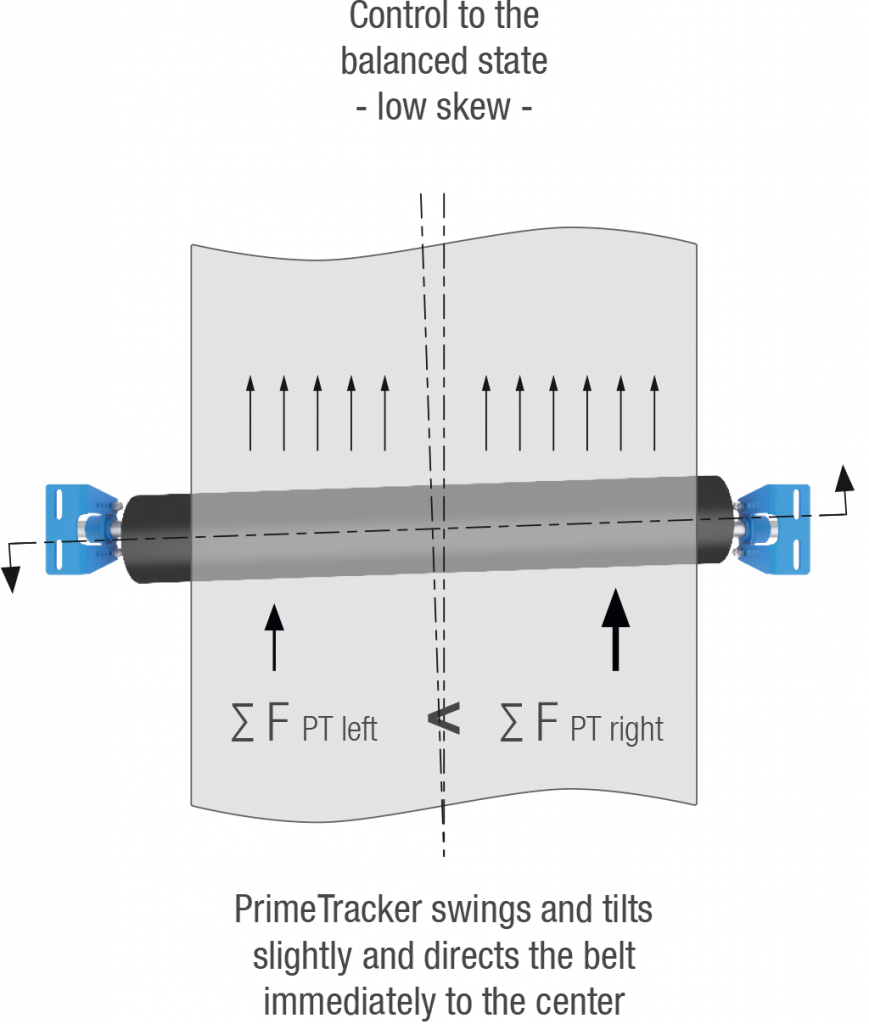
In case of strong misalignment
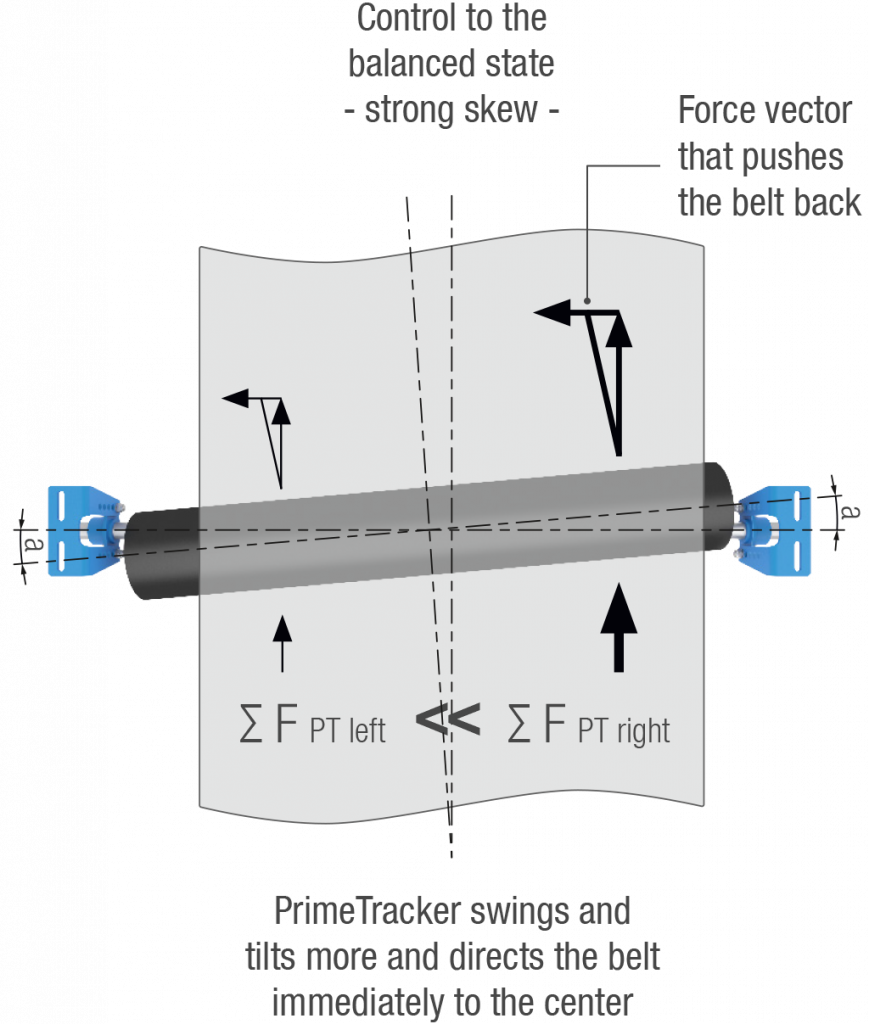
Balanced
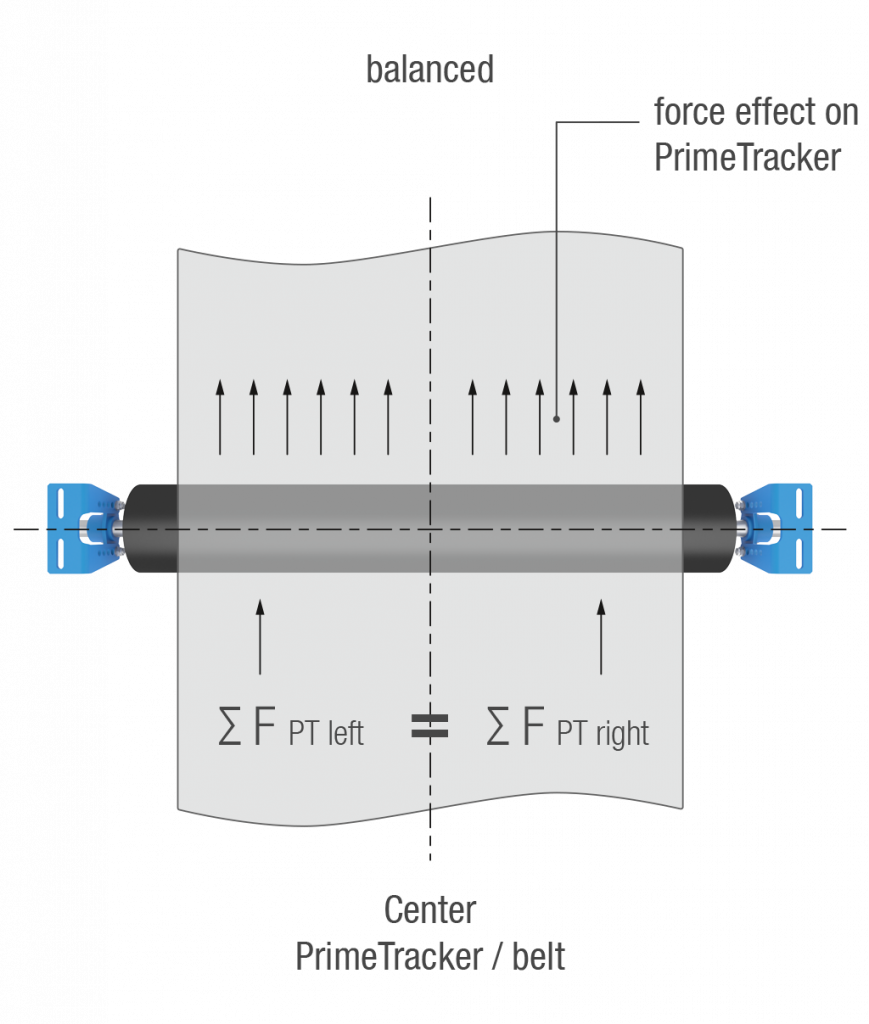
Easy installation and low maintenance effort
The E-PrimeTracker can be easily and quickly installed with minimal effort and is mounted at a distance of 3.5 times the belt width in front of the head pulley. It can be installed above or below the belt. The PrimeTracker is preferably installed on the clean side of the conveyor belt and is available for belt widths ranging from 500 to 2000 mm.
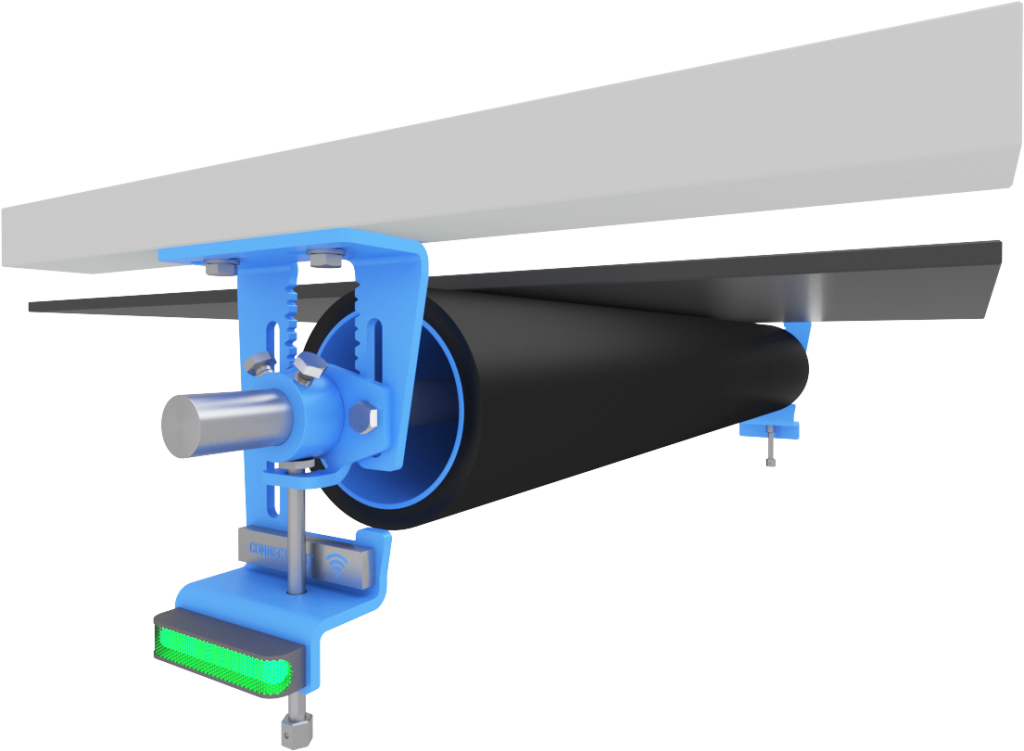
Below the belt
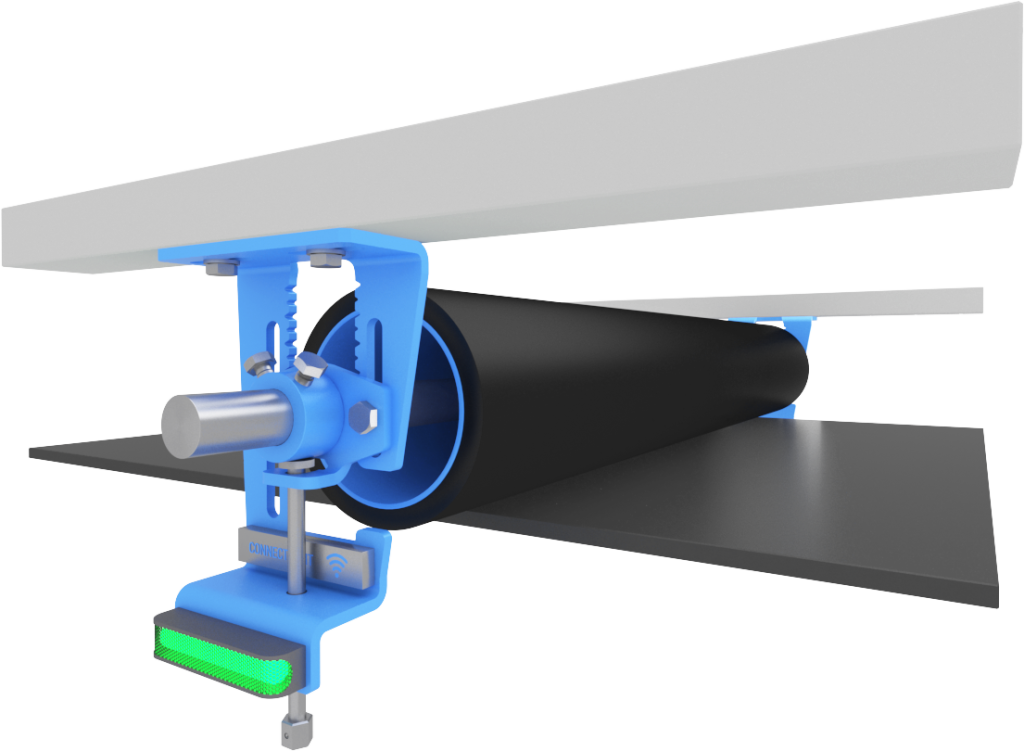
Above the belt
Easy installation and low maintenance effort
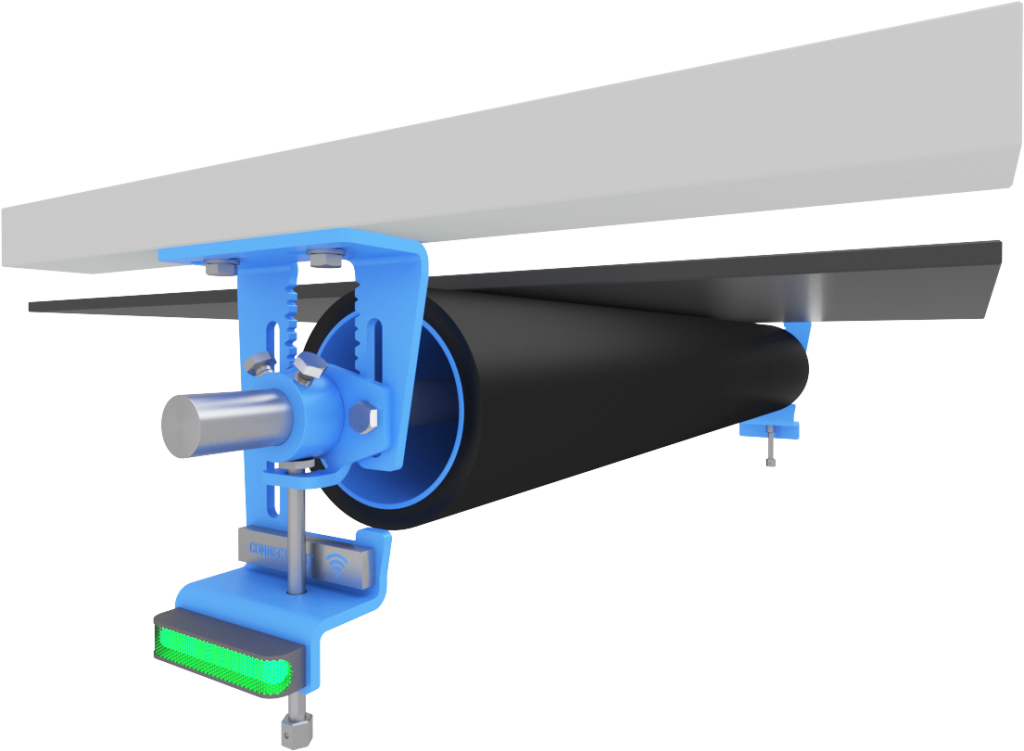
under the belt
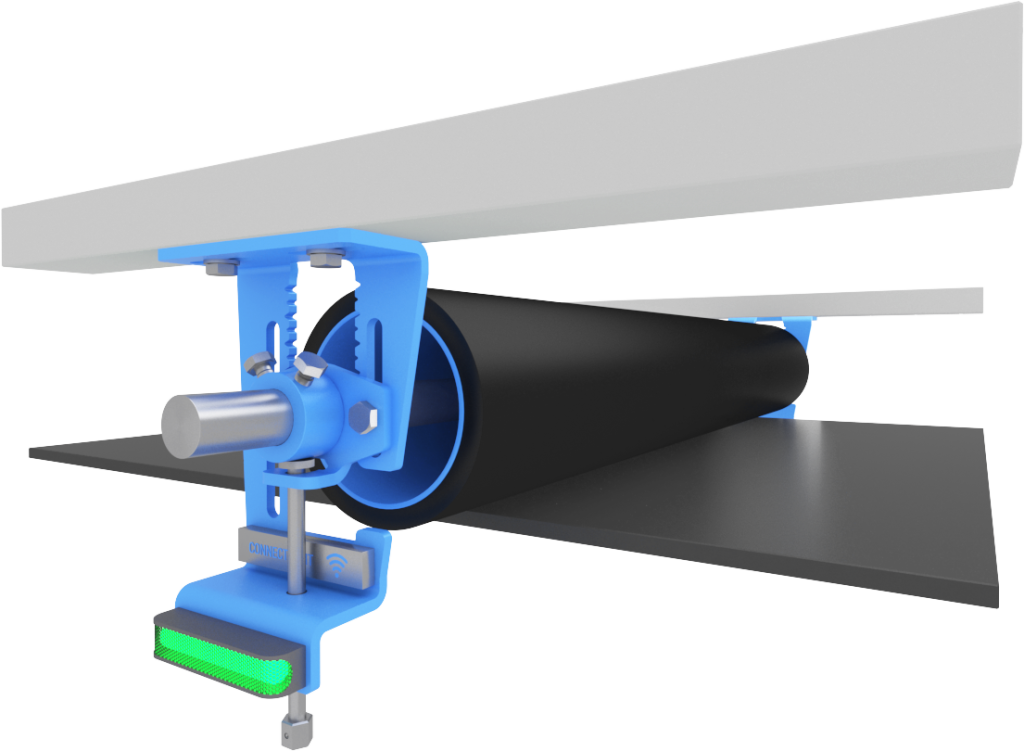
top of the belt
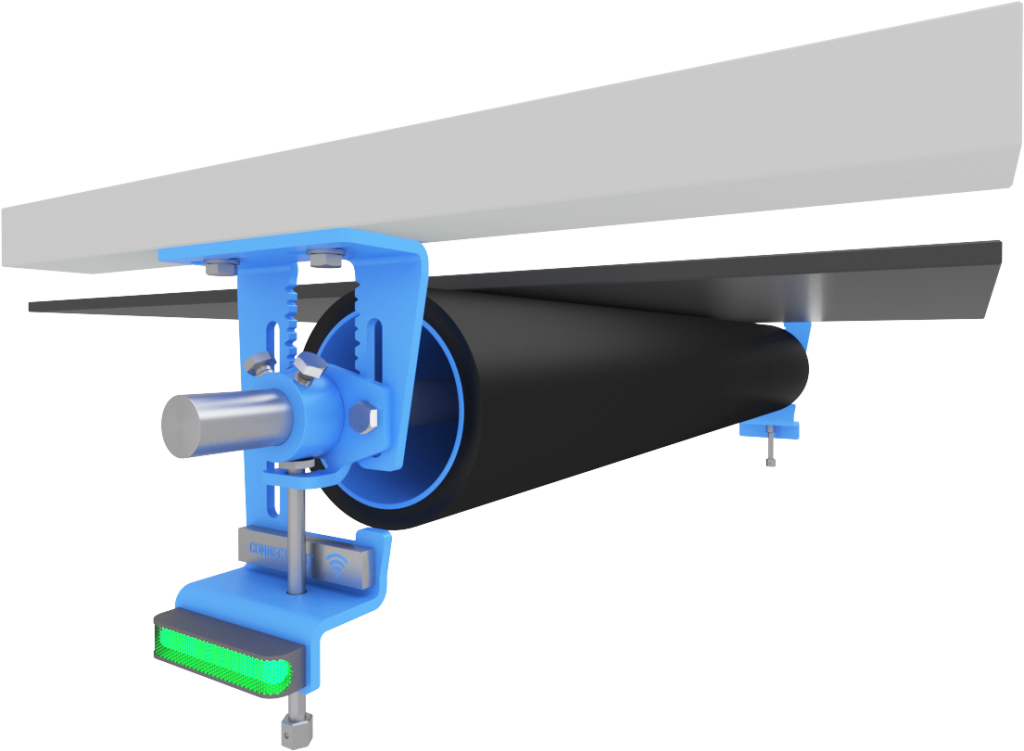
under the belt
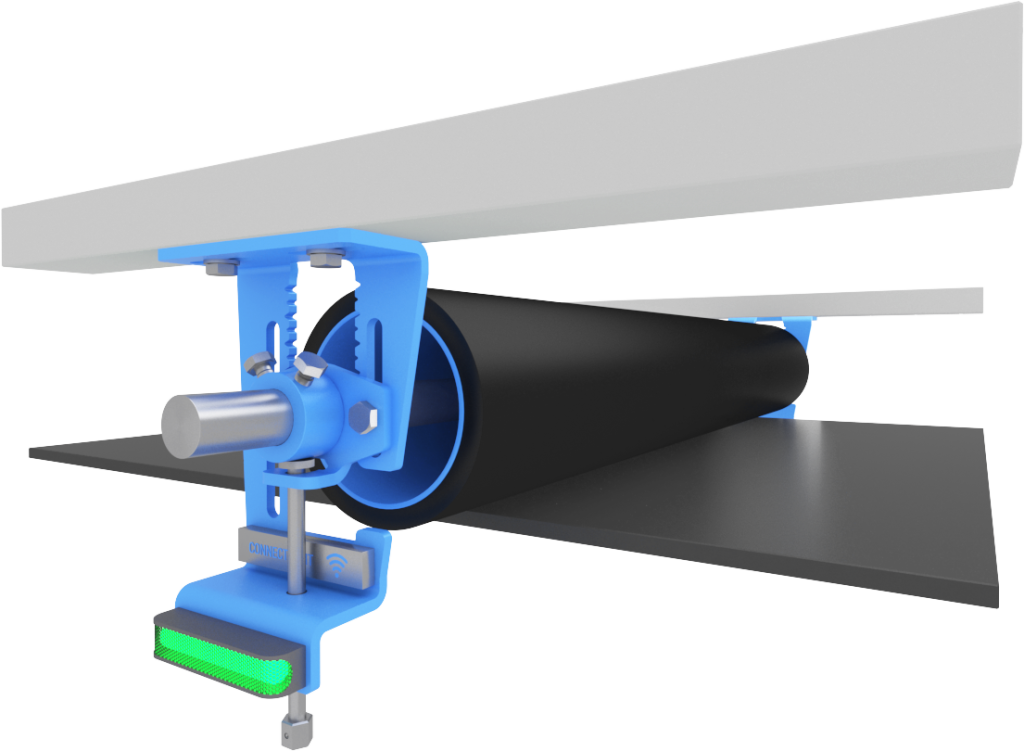
top of the belt
The E-PrimeTracker can be easily and quickly installed with minimal effort and is mounted at a distance of 3.5 times the belt width in front of the head pulley. It can be installed above or below the belt. The PrimeTracker is preferably installed on the clean side of the conveyor belt and is available for belt widths ranging from 500 to 2000 mm.
Knowing what happens when
Detecting critical events and high wear operating conditions in a timely manner is crucial for avoiding high and costly maintenance work or plant downtime.
With the E-PrimeTracker 4.0, ScrapeTec offers a further development of the already proven PrimeTracker. Its self-regulating function on conveyor belts corresponds 1:1 to that of the PrimeTracker. The “E” stands for the electronic added value of the device that ScrapeTec developers have integrated. In addition to its unique mechanical belt regulation properties, the E-PrimeTracker is equipped with additional sensors. In line with condition and belt monitoring, predictive maintenance, and Industry 4.0, it detects, for example, belt misalignment, belt position, belt speed, and the condition of the belt connection and wirelessly transmits this data to mobile and stationary monitoring systems for maintenance purposes.
In addition, the E-Prime Tracker also visually signals the condition of the belt run via a light unit attached to the roller, enabling the timely detection of critical events on site. Employees can intervene in time and avoid belt damage or downtime.
With the E-PrimeTracker, you know what happens when and increase the efficiency and safety of the conveyor system.
Advantages
- Sensor-based detection of belt running condition
- Detects critical events in a timely manner
- Prevents belt damage and conveyor downtime – Predictive Maintenance
- Remote monitoring via smartphone app – Mobile Monitoring
- Reacts immediately even at the slightest misalignement
- Contributes to long-term optimization of plant efficiency
- Suitable for Condition Monitoring and Industry 4.0 systems
- Directs the belt with very low friction and small forces → high service life
- Does not “wait” for the tracker to tilt vertically, as with other systems, but reacts beforehand
- Works perfectly in reverse operation
- Easy installation
- Maintenance-free
- Special central bearing, very durable
- Guarantees optimal belt position at transfer points, making spillage at transfer points impossible in combination with AirScrape
Knowing what happens when
Detecting critical events and high wear operating conditions in a timely manner is crucial for avoiding high and costly maintenance work or plant downtime.
With the E-PrimeTracker 4.0, ScrapeTec offers a further development of the already proven PrimeTracker. Its self-regulating function on conveyor belts corresponds 1:1 to that of the PrimeTracker. The “E” stands for the electronic added value of the device that ScrapeTec developers have integrated. In addition to its unique mechanical belt regulation properties, the E-PrimeTracker is equipped with additional sensors. In line with condition and belt monitoring, predictive maintenance, and Industry 4.0, it detects, for example, belt misalignment, belt position, belt speed, and the condition of the belt connection and wirelessly transmits this data to mobile and stationary monitoring systems for maintenance purposes.
In addition, the E-Prime Tracker also visually signals the condition of the belt run via a light unit attached to the roller, enabling the timely detection of critical events on site. Employees can intervene in time and avoid belt damage or downtime.
With the E-PrimeTracker, you know what happens when and increase the efficiency and safety of the conveyor system.
Advantages
- Sensor-based detection of belt running condition
- Detects critical events in a timely manner
- Prevents belt damage and conveyor downtime – Predictive Maintenance
- Remote monitoring via smartphone app – Mobile Monitoring
- Reacts immediately even at the slightest misalignement
- Contributes to long-term optimization of plant efficiency
- Suitable for Condition Monitoring and Industry 4.0 systems
- Directs the belt with very low friction and small forces → high service life
- Does not “wait” for the tracker to tilt vertically, as with other systems, but reacts beforehand
- Works perfectly in reverse operation
- Easy installation
- Maintenance-free
- Special central bearing, very durable
- Guarantees optimal belt position at transfer points, making spillage at transfer points impossible in combination with AirScrape